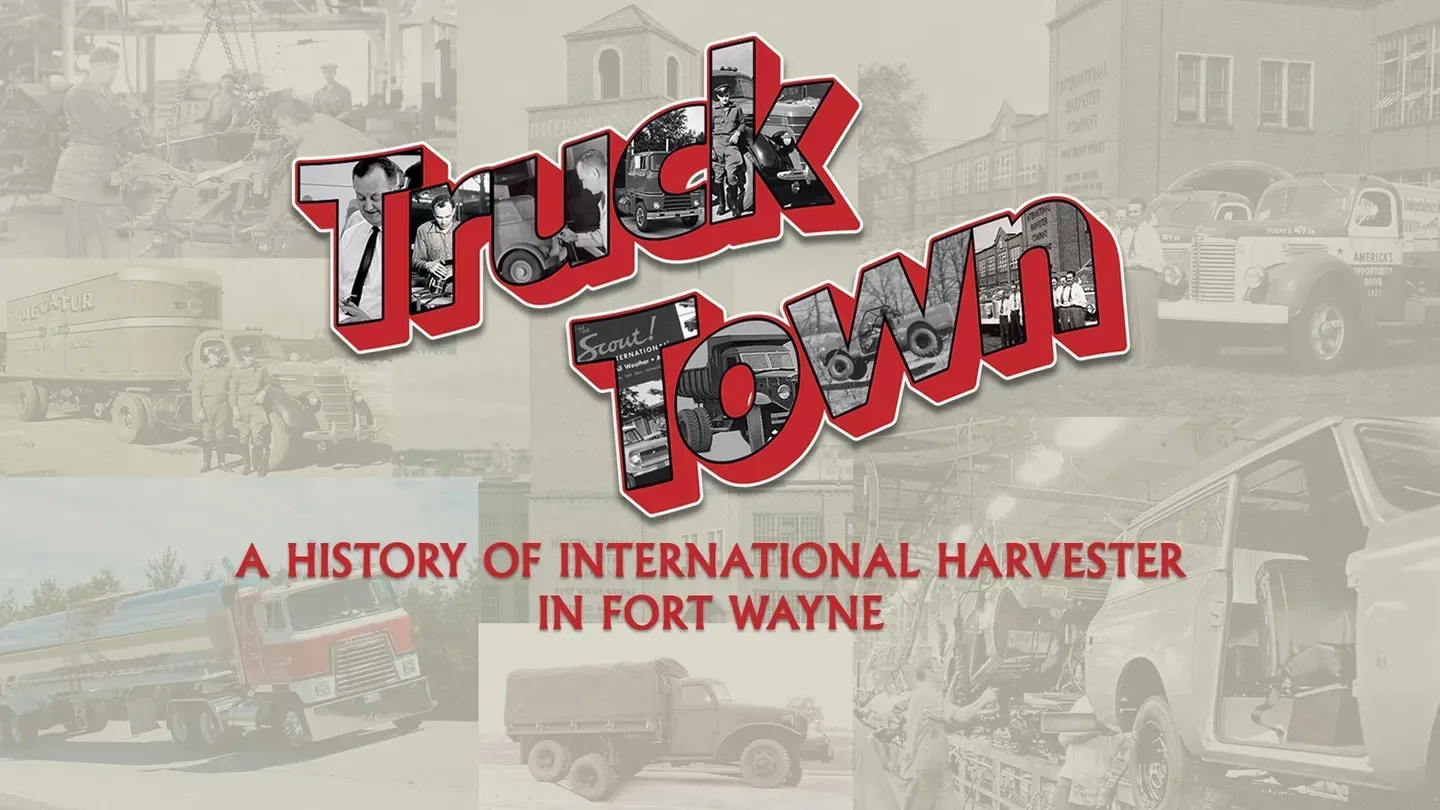
Truck Town - A History of International Harvester in Fort Wayne
Truck Town - A History of International Harvester in Fort Wayne
Special | 1h 56m 53sVideo has Closed Captions
Learn how Fort Wayne earned the reputation as the “Heavy Duty Truck Capital of the World."
Go on a journey through time, from International Harvester's first trucks made in Fort Wayne in 1923, through Harvester’s contributions to the WWII war effort, on to the decades that trucks of all sizes were designed, tested, and engineered in the “Heavy Duty Truck Capital of the World.”
Truck Town - A History of International Harvester in Fort Wayne is a local public television program presented by PBS Fort Wayne
Hanning and Bean Enterprises Inc., 3Rivers Federal Credit Union, O’Rourke-Schof Family Foundation, Koester’s Body & Frame Shop, Selking International Trucks, and the City of New Haven, Indiana
Truck Town - A History of International Harvester in Fort Wayne
Truck Town - A History of International Harvester in Fort Wayne
Special | 1h 56m 53sVideo has Closed Captions
Go on a journey through time, from International Harvester's first trucks made in Fort Wayne in 1923, through Harvester’s contributions to the WWII war effort, on to the decades that trucks of all sizes were designed, tested, and engineered in the “Heavy Duty Truck Capital of the World.”
How to Watch Truck Town - A History of International Harvester in Fort Wayne
Truck Town - A History of International Harvester in Fort Wayne is available to stream on pbs.org and the free PBS App, available on iPhone, Apple TV, Android TV, Android smartphones, Amazon Fire TV, Amazon Fire Tablet, Roku, Samsung Smart TV, and Vizio.
Truck Town: A History of International Harvester in Fort Wayne was brought to you by Hanning and Bean - a commercial real estate and property management firm invested in the development of Northeast Indiana.
Proud to support PBS Fort Wayne in preserving the legacy of International Harvester.
In 1935, Three Rivers Federal Credit Union began as a financial cooperative for the hardworking employees of International Harvester.
Committed to supporting the people, places and ideas that make our region home.
3Riversfcu.org.
O'Rourke-Schof Family Foundation.
Proud to bring the International Harvester story to the community.
Additional funding provided by Koesters Body and Frame Shop, Selking International Trucks, and the City of New Haven.
[upbeat music] Fort Wayne is a truck town, [upbeat music] and it all started here at the International Harvester truck factory.
So somebody said, “Well, you oughta go into Harvester.
They're trying to hire people.” Many people thought a job with Harvester was a job for life.
I was going to work for the International Harvester.
My employee number was 24936.
Interviewed out of high school.
This was my second job out of high school.
I started second shift.
Of course, you had to be on second shift for quite a few years before you ever got on days.
I started in machine shop.
Hired in as just a detailer to begin with.
Handyman.
Go get this.
Go get that.
Hired in as a steno two.
The forge shop on third trick.
Learn real quick why people wear hardhats.
I work in the blueprint room and the vault.
I started out on the broom.
I was a janitor on third shift.
Mopped and washed every floor in that building.
Key punch operator.
I started a key punch, and that's all obsolete now.
I started out setting engines in the Scout on the Scout line.
The line work was tough, and it was hard.
I built some muscles up doing that job.
Just gave me the job that maybe has the most overtime and your highest assembly rate.
And I ended up down the basement on axle assembly.
You start in with low seniority.
You worked the hard jobs Opportunity to do a lot of different things.
I worked in the hot room.
You might be a brake engineer one day, but you might be a chassis engineer the next day.
In the cold room.
I was a reliability engineer.
Special equipment engineering.
I worked in SE for a while.
I worked in the chassis group for a while.
I was a clay modeler.
You were able to move around from one department to the next.
I went to warehousing for about five years.
In the brake department.
I transferred over to the machine shop.
Cab mount, parts chaser... Building housings.
Rail fields, and I worked inside.
I worked outside.
The top mounts.
Did brake work.
I did steering.
Machine shop where they used to make the parts.
Body mount, which you had.
watch your fingers.
You had the timely, quick and you had to keep up the line.
I was an expediter, actually.
I was a buyer's assistant for a while.
I was in expediting.
Planning department.
Went to timekeeping, which I loved.
I did all the painting for design group.
Then I worked engine mount and then I got in on the finished body line.
In my 40 years, I had 16 different jobs.
“Well, Grandpa,” he says, “you never were on a job more than a couple of years until the end.” He says, “Couldnt you hold a job?” [country music] This is only a handful of people representing the tens of thousands of people who worked at International Harvester in Fort Wayne, Indiana, throughout its 92 year stay in the city.
It was a dependable place where a person could get a good paying job and count on working there until the day they were ready to retire.
I started there in ‘66 in road test as an M140 mechanic.
I hired in ‘65.
1968.
Late ‘59.
Early 60.
‘60-61.
Something like that.
January of 1963.
Started in 1963.
March of 1966.
1966.
1966.
1970.
I started in 1986.
February of ‘98.
1941.
I worked here a little over seven years.
I was here 30 years.
35.8 years.
37 years.
And I retired with 37 years.
Ended up working 37 years.
Put in 39 years.
39.7 years.
40 years and a couple weeks.
I had 41 years service.
41.9 years.
So I just got my 50 years in.
I never thought I would last two or three years.
I made a career out of it.
Through a good many decades of the 20th century.
People like these used their minds and hands to conceive and build vehicles that help make America.
They helped a nation fight her battles.
They kept America moving.
They gave hardworking Americans something to look forward to on the weekends.
And captured the hearts of many.
<Engine sounds> [upbeat music] I love old trucks.
Ive been around trucks all my life.
I'm an IH man, I'll tell you that.
Any old car, any old truck is of interest to someone.
Somewhere along the line, a truck was involved in everything except the air you breathe.
[Music] If I can design vehicles for the rest of my life, I'll be the happiest camper you ever saw.
At times, they had 10,000 people working.
The best hourly jobs in the county.
That was good money.
On the line, we made good pay.
At the end of the week, there were some good rewards.
I liked the money.
I enjoyed the pay I think most of all.
You know, really.
When I come out of school and I went to work as a trainee, I think I got $3.28 or $3.29 an hour.
When I left there, it was close to $7 an hour.
Yeah, it was big money.
I made $15 a week.
If you have a family member, that was a natural pull.
They liked to have families there because they would get on each other's backs if they didn't do a good job.
But they weren't 100% in their attendance.
If that guy is a good worker, maybe his son's a good worker.
My grandfather worked here.
My uncle worked here.
My wife had several uncles who worked here.
I was the second generation.
My daughter worked here, was the third generation.
I worked from 11:00 at night till 7:00 in the morning, and class started at 8:00.
It was hard work.
As you got older, you didnt want to do it.
International Harvester says its production will increase by 50% next month when it begins work on 1800 new Paystar trucks for Iraq.
Production was at its peak.
We were producing 205 heavy duty trucks a day.
Most that any heavy duty truck plant in the world ever did.
We were the king of cab over engine trucks.
A lot of manufacturers just build the truck and then we made it the way you wanted.
Harvester built it the way you wanted right from the beginning.
I get around Fort Wayne down there and I would just drool, because that was the truck capital of the world and International in my opinion is the best truck ever built.
When they built the Hoover Dam, my gosh, they used all Harvester trucks.
I started collecting Scouts in the early seventies.
It was a strong vehicle and it was stiff suspension, but was very strong.
Farmers absolutely loved it.
They know two names.
They know Farmall tractors and they know the Scout.
It wasn't fast, but it was a lot of fun.
Very simple vehicle to work on.
After you work on it all winter and you get it to where you can take off and drive it, turn the radio on, go over to a friend's house.
It's pretty cool.
There was a lot of pride...built the Scouts.
A lot of people not only built them, but they drove them.
I'd say it was probably the best place to work and we were very proud of the product that we produced.
We were like one big family.
I loved International Harvester.
I breathed it.
I ate it.
They treated me super.
They paid me very, very well.
I loved it.
[rock music] [music] In the 1831, 22-year-old Cyrus McCormick perfected a horse drawn mechanical reaper for harvesting grain.
This invention would revolutionize agriculture around the world.
McCormick used innovative sales and marketing practices to make his Harvesting Machine Company one of the leading manufacturers of farming equipment in the U.S., producing over 50,000 reapers a year.
After his death in 1884, Cyrus McCormick Jr. stepped in to take the reins from his father.
But there was a crowded field of competition with one of the largest competitors being the Deering Harvester Company.
Cyrus Junior was tired of fighting with his arch rival, William Deering, and there were 300 other reaper makers out there and it was just difficult to do business.
So they merged to form International Harvester with three other reaper makers.
The 1902 merger of the two major manufacturers McCormick Harvesting Machine Company and Deering Harvester Company, along with three smaller manufacturers, created an industrial juggernaut: The International Harvester Company.
Immediately after the merger, Harvester owned an 85% market share.
[music] Harvester got into the truck manufacturing business by way of the automobile.
Even though the McCormicks and the Deerings had built empires around horse-drawn farming implements, both companies have been working on self-powered vehicles during the 1890s.
In the years following the merger, the first tractor appeared in 1906, followed by the auto buggy in 1907.
This “horseless carriage” resembled many of the first automobiles being developed at the time.
This led to the development of a more truck-like vehicle called the “Auto Wagon” which debuted in 1909.
We say the auto wagon was developed for farmers, but there are hundreds of pictures of them already as delivery vehicles serving every industry right from the start.
So it wasn't strictly a farm product at all.
The leadership in International Harvester soon saw the potential to branch out from agricultural products to tap into this new market for delivery vehicles.
A factory in Akron, Ohio, was converted from making farm implements to making these new motor vehicles.
Then in 1912, they started building what they called motor trucks, and that was really where they got into the truck business for the first time.
Even though the company identity was still strongly tied to the McCormick-Deering names and the primary focus remained on the farming business, This new venture was charting a course for the future: International Harvester Company was now a truck manufacturer.
[music] By 1910, International Harvester Company had become the nation's largest producer of light trucks, and it was now the fourth largest company in America.
The early years of the 20th century witnessed a boom in vehicle production.
More and more businesses discovered how useful trucks could be for delivering milk, food, goods and a variety of wares.
As they started with auto wagons, they quickly took over a plant over in Akron, Ohio.
But by the teens, that was being outgrown and they had to expand somehow.
Akron did fine for a number of years, but it was landlocked.
There was no room to expand the dimensions of the plant, Expanding sales paired with an unexpandable factory created quite the dilemma for the International Harvester Company.
To alleviate the situation, a former Champion farm equipment factory in Springfield Ohio, was reconfigured to supplement the production of motor trucks.
At the same time, the board resolved to further expand their manufacturing capabilities by constructing a brand new factory, solely dedicated to producing motor trucks, that would have the capacity to fulfill the increasing orders.
A nationwide search was underway to find the ideal location.
Representatives from Harvester began contacting city officials and business leaders in 26 different localities.
In November 1919, one of those locations was Fort Wayne, Indiana.
They approached the Fort Wayne Chamber of Commerce.
Charles Finch was the president and told them that they were looking at Fort Wayne as a possible site for a new heavy duty truck plant.
Harvester said we're looking to build a plant that's going to cost between four and $5 million.
We're going to employ 4 to 5000 employees.
We're going to produce about 30,000 trucks per year, which is just an astronomical number.
Now, the bad news is we want you to form a corporation and fund it with $750,000 to ensure that the other things we need, like public services brought to our site, can be accomplished.
They wanted streetcar service run to the plant site.
They also wanted a beltline run to the plant site that would come off of the main railroad tracks.
And this beltline could be used equally by the Wabash Railroad, the Nickel Plate Railroad, the New York Central and the Pennsylvania Railroad.
The Fort Wayne Chamber of Commerce got to work by forming the Greater Fort Wayne Development Corporation to raise the necessary $750,000 The raising of this $750,000 was a Herculean feat In 1919, $750,000 was a whole lot of money.
they ended up getting over 200 people in Fort Wayne and businesses to contribute to the fund.
And instead of raising $750,000, they raised $1 million.
[music] In April of 1920, International Harvester Vice President Herbert F Perkins shared with the Board of Directors a unanimous recommendation from the manufacturing department to choose Fort Wayne as the location for the new motor truck manufacturing plant.
A site was chosen three miles east of the city and 143 acres of land was to be purchased at a cost of $700 per acre.
The site that was decided on for International Harvester, which we now call the East End Industries area, was really just farmland.
My grandfather on my mother's side - that's where they live.
That was their family farm and they sold the farm to International back in 1920.
The big news was announced in June of 1920. International Harvester would be bringing their motor truck manufacturing factory to Fort Wayne.
The plans called for a factory and two other buildings with 193,000 square feet under roof.
One impressive architectural element of the Fort Wayne works would be a colossal rectangular tower bearing the name “Internationa” on all four sides.
What a lot of people don't realize is that the tower, which is 150 feet tall, housed a 100,000 gallon water tank.
Rising high above the surrounding farmland, the tower could be seen for miles away.
It would become an icon of not only the International Harvester Company, but also of Fort Wayne as a home for industry.
Shift changes were signaled by a loud steam whistle atop the powerhouse.
The distinct tone could be heard for miles around the factory.
Willard Bryce Shull was born in 1921, two years before the plant was completed.
He and his family lived near the plant and regarded the whistle to be a community timepiece.
We lived by that whistle.
I lived not too far down about two blocks.
I knew the timing of, people went to work and when they got off.
The last whistle was at twelve oclock.
That was the last one until seven in the morning.
I heard that whistle for years, but I never knew I was going to be working by it.
[music] Construction began in May of 1922.
The first truck would roll off the Fort Wayne works assembly line in December of 1923.
Workers would produce 433 trucks by the end of the year.
From this point forward, Fort Wayne would be a truck town.
Once the full capacity of the factory came on line in 1924, a total of 6,831 trucks were made that year.
The Model 103 was one of the new truck models being built at the new plant.
The rugged truck with a 10,000 pound maximum capacity marked the beginning for Fort Wayne.
Things were going well in Fort Wayne in 1924.
Plans were announced to expand the works in order to increase production capacity.
By 1925, the International Harvester Company had earned its place as the country's largest manufacturer with a full line of trucks.
The Akron works closed that same year.
Truck production was now divided between Fort Wayne, Indiana, and Springfield, Ohio, with a third truck plant serving Canada in Chatham, Ontario.
Those factories combined to produce about 15,000 trucks in 1926.
In 1928, total production reached a record 40,000 units.
International Harvester makes a complete line of trucks, the best that men, money, and more than a century of manufacturing experience can build.
The factory at Fort Wayne, where heavy duty models are manufactured.
There are Internationals to meet every hauling need, dependably and economically.
The plant complex was expanded to complement the assembly of trucks by adding a forge for making parts and an 80 acre proving grounds facility to test the trucks under extreme conditions.
Really, when the Depression hit in the fall of 1929, it took a while for it to catch up with Fort Wayne.
We kept sailing along for a while because of the diverse industrial base that we had here.
But eventually, of course, it caught up with Fort Wayne, too, and caught up with International Harvester as well.
The International Harvester Company went from a high of 51,000 trucks produced in 1928 to a Depression era low of just 17,400 in 1932.
During the lean years of the early 1930s, the Federal government turned its resources toward public works and infrastructure projects.
These big projects called for big trucks.
We supplied 80% of all the trucks to build the Hoover Dam, which was the biggest public works project in the country's history.
in this early stage of the work, millions of yards of rock and dirt were to be removed.
A fleet of over 100 International heavy duty trucks was selected by the six companies summer and winter working 24 hours a day to choking dust and fighting winds in temperatures as high as 120 and in cold often below freezing.
Things were much heavier duty.
We were building really big trucks.
Drastic changes from the from the ‘20s.
Whatever the destination, these heavy duty trucks are ready and able to go.
Such flexibility and ability to work and never get equaled by any other form of transportation.
And the adaptation of trucks to specific jobs is still in its beginning.
[dramatic music] The decade of the 1930s would end under the shadow of a dark cloud of uncertainty cast by the escalating conflict in Europe and Asia.
By the summer of 1940, France had surrendered to Germany and Great Britain was under siege from the relentless Nazi air attacks.
We were anticipating that we were going to get into the war and we were planning at least ahead of time.
The M-1-4 and M-2-4 were in response to an invitation to bid for a contract for the rearmament programs that were coming in 1939 and 1940 because we knew we were going to be in a war sooner or later.
So they were building up our military and making orders of different kinds of equipment.
[dramatic music] December 7, 1941, America was stunned by the news that war had come to the US in a surprise attack at Pearl Harbor.
Logistics would be a vital part of supplying allied troops with everything they needed to win the war.
To do the job, it would take thousands of trucks from every vehicle manufacturer in the U.S.. Mobility is the essence of modern war, and America's motorized forces must be kept rolling over at the Fort Wayne Works, plant facilities are being used for the manufacture of military trucks.
Wartime production had begun.
Fort Wayne continued to build heavy duty trucks and some medium duty models.
Springfield built half-tracks, along with light duty trucks and early four-wheel-drive vehicles.
Fort Wayne Engineers designed vehicles to meet military specifications.
Then prototypes underwent rigorous testing at the Fort Wayne Proving Grounds.
The performance of a military unit is tested on the proving ground just the same way all the guesswork is taken out of a standard truck.
International trucks are rolling on the Burma Road and driving across the hot sands of Africa and doing yeoman service with friendly foreign powers, all under the toughest possible conditions.
We tested trucks that were going to be an even more difficult situations than bad roads in Europe or wherever they were headed.
One of the government-designed heavy duty military vehicles being built at the Fort Wayne Works was the M-5-6; The M-5-6 was probably the best deuce and a half built during the war, especially the M-5H-6, which was a specialty version that the Marine Corps used because it was a high mobility six by six.
[dramatic music] The US Army had a major concern with the thousands of trucks it was putting into service.
Once they were in the field of battle, there was still a need for maintenance and repair.
With such a large fleet of vehicles under their command.
The Army came to the manufacturers asking for a qualified mechanics willing to serve.
International responded by recruiting from its factories and dealerships, putting together and training a group of field mechanics that would become known as the Harvester Battalion.
The 134th Ordnance Maintenance Battalion would go on to be cited for meritorious services, repairing trucks, tanks and halftracks on the front lines in France and Germany.
[military music] Company-wide, over 13,000 International Harvester employees enlisted in some form of military service during the war.
This left thousands of vacant jobs that needed to be filled to meet the wartime production demands.
World War Two provided women and minorities with new employment opportunities, unlike any other time in our nations history.
We had an anti-discrimination policy that we issued in 1919.
We were way ahead of our time, but our plants were not very integrated until the war.
The Fort Wayne Works gained a tenuous connection with one of the legendary Tuskegee Airmen.
Thanks to former employee Maxine Hall.
Her husband, Charles B.
Hall, was the first African-American to shoot down a Nazi aircraft, during a dogfight in Italy.
He would go on to fly 198 combat missions, earn the rank of Major, and receive the Distinguished Flying Cross.
[music] [music] Eventually all the hard work would pay off.
The allies would see victory in Europe and Asia.
Americans celebrated as loved ones returned home and life slowly fell back into its normal pace.
For the International Harvester Company the return to normal would bring record sales.
In 1948, truck production hit a new high of 172,000 vehicles and Fort Wayne did its part by building 46,955 trucks.
As America turned the corner from the war-fueled 1940s, into the domestic baby-boom decade of the 1950s, the International Harvester Fort Wayne Plant complex had grown to include 31 buildings, with 40 acres under roof, on a total of 124 acres of land.
By 1950, half a million trucks had rolled off the assembly line of the Fort Wayne Works.
Employment levels fluctuated between fifty-five hundred and six thousand workers.
The increased sales brought on by postwar optimism and a booming economy caused some growing pains at the Fort Wayne Works.
Management wanted design and engineering to come together in one location.
Ground was broken in July of 1950 for the construction of a new Motor Truck Engineering Department and Laboratories in Fort Wayne.
This 250,000 square foot, 8 million dollar facility, would be a place where planning, design, and testing all came together.
It's critical to have all those people in the same place on the same page.
Everything was designed here and for the most part, built here.
You look under the hood.
There's almost no room for another anything in there.
And our designers would be arguing about the slope of a hood, and the engineers would be telling them about all the other pieces of equipment that still need to go under that hood.
To make one truck, you've got hundreds, literally thousands of parts that go in into that truck.
[music] In order for all of these parts to fit together, it takes careful planning, precise drawings and a whole lot of engineering knowhow.
All this has to come together and work together to build a vehicle that doesn't fail, you know, has high reliability.
And so we would have hundreds of engineers to design one truck, different kinds of engineers, some electrical, some mechanical, some test engineers.
We did all the new product development, so all the new trucks, we did all the sustaining engineering.
To develop a truck.
It takes years to do it right.
And even then, youre accelerated testing, A lot of design, a lot of tests, redesign, retest, validate, and then you gotta make sure that can all be produced It takes hundreds of people, thousands of man hours to develop a product like that that's acceptable in the marketplace, is safe and reliable and durable.
How many miles should this last?
What kind of roads is it going to run under?
What's it going to haul?
Those sorts of things.
How is the customer really going to use it?
Creates the specification and then the engineers sit down and they start to develop the truck and it's really developed on paper.
And at some point it goes from kind of the specifications to a set of drawings.
These drawings had to be very precise and very detailed.
Not just major components, but every seemingly insignificant screw, washer, nut and bolt had to be represented.
Every part that we used it took an army of engineers and draftsmen to produce the drawings that would be needed for all phases of development, testing and production.
This all took place in one huge space at the engineering center in Fort Wayne.
It was called the drafting room, the design room.
And when I started that was all open and, and there was eight foot and ten foot and 12 foot drafting boards but what was going on in there was all the hard work of getting drawings ready or bills of material ready or detailed drawings or assembly drawings of how to build those products.
We had hundreds of engineers in there and designers and detailers doing that work in there.
it starts with putting it on what we call the layout, either the whole truck or portion of the truck where that part's going, how does it fit with everything else going around there?
and the guys start putting it together, putting all those parts together, and invariably they start saying, This isn't going to work.
You can't put this together in the manufacturing facility.
Engineering would design a part and then if they had trouble with it on the line, they blamed the guys on the assembly line for not knowing how to put it on and theyd blame engineering for not knowing how to design it.
It might be surprising, but sometimes engineers design things that can't be put together.
Even if all the parts actually fit together, it doesn't necessarily mean they will work together.
Then you start to test it.
And that's where you start to find out, hey, you know, we did this virtually, but in the real world, these temperatures are higher or the stresses are higher.
And so then you go through kind of a phase of redesign and prototype and redesign.
This is taking years, a typical truck, if you could do it in four years, that's pretty good.
Most new products would take five years.
And then you actually go to the manufacturing plant, probably a year before youre, you have everything tooled up.
Can we build it in the plant?
And then that last year is really just preparing for production.
Before a truck could go into production, every part had to be tested.
First, the parts were tested on an individual level, then, assembled units like transmissions and engines were tested for functionality and durability.
Finally, a complete prototype truck was submitted to various kinds of testing under extreme conditions.
Engineers created different types of environments for testing the limits of the products they were designing.
The Shaker Lab was meant to simulate the jarring conditions a truck might encounter on a construction site or driving thousands of miles on rough roads.
You could shake a hood, you could shake a radiator, you could shake a cab and it really simulated, if you think about going over railroad tracks as an example.
You can drive over railroad tracks so many times a day.
But if you can get over 100 times a day, that's probably a lot to drive over a railroad track.
Literally, you could drive over a railroad track on a shaker every 5 seconds.
Because International trucks were used worldwide.
They had to be able to function in some of the most extreme temperatures on the planet.
The Fort Wayne engineers created special lab environments to simulate sweltering heat in the hot room and subzero temperatures in the cold room with the capacity to go as low as -100 degrees Fahrenheit.
I'd say the majority of the tests were 40 below.
Forty below zero, a soft seat is rock.
A rock.
These extreme temperatures not only tested the limits of what a truck could endure, but also the limits of what the human body could endure.
The cold room had specific guidelines to prevent serious injury to the personnel working inside.
Special gear had to be worn and strict time limits were observed, depending on the testing temperature.
Time limit in the cold room.
I think was 15 minutes.
15 minutes, 15 minutes, Then, when you were 70 or 80 below, like 5 minutes.
Yeah, that was in an eight hour period.
In order to design and build a reliable and safe truck, engineers often had to bring components to the point of failure to find design flaws, reveal weaknesses in materials, or establish safe operating limits for a product.
This involved using some creative methods to invent tests that could push products beyond their breaking point.
Another factor that affected truck development was government regulation.
Vehicle manufacturers had to meet certain federal standards before they could put a truck on the market.
This required engineers to perform specialized testing under very strict standards.
It was a large part, through the eighties, nineties and even up till now, is the government regulations, a lot of investment to meet the regulations.
Every three or every four years, we had a new emission standard and so we would have to go in and there'd be a new engine installation, a new radiator installation, And so it became a large part of what we did here.
The brake regulations were the same thing during that time frame.
They wanted them shorter and shorter.
For all for great reasons.
Right?
We want trucks that can stop When we first started did brake tests, we didn't have the anti-skid systems and you'd have to hit the brake pedal hard enough to stop as quick as you could without locking the wheel.
And you kind of built your way up to speed.
Well, when they came out with this anti-skid brakes, we didn't have any more of that.
You went out and you did a 60 mile an hour panic stop, we call them.
And you talk about something, you talk about something to make you pucker up on that seat.
You come around that curve.
As soon as you hit the flat, you had to stab that brake and hope it worked because you.
[laughter] Thats right.
That truck, bear in mind, you're going down the road at 80,000 pounds.
That's the max.
But it had to stop in X number of feet.
The Cargostar was short, and that thing would jump from one axle to the other.
You remember that truck?
Yeah.
Well, it just about kill you.
It was crazy.
I know they built a 9670 with a real short wheelbase one time.
Yeah, I remember that.
And it would almost go on its nose when you guys hit the brakes.
Yeah, yeah.
The rear end would come off the ground.
So they didn't sell them.
They turned around.
We went to a longer frame on it.
[50s music] The proving grounds, a very important external facility with a 1.2 mile banked oval track, was where testing was done on fully assembled vehicles under extreme driving conditions.
The purpose of the proving grounds test track was really just to speed up testing.
These trucks, some of them will last a million miles.
How do you put a million miles on a truck in a few years?
You can't.
And so you accelerate test them.
That's what we did at the test track.
At the proving ground track at Fort Wayne, Indiana.
Drivers wear them out if they can.
There's what we call events, whether it's a turning event where you turn the truck or whether it's going over a rough bump or whether it's putting it through twist course.
Those are things you can accelerate at the test track.
Areas where we can fill up and run trucks through water to speed up rusting or corrosion and things like that.
The Belgian blocks, scientifically constructed rough roads deal out their punishment to the springs, the steering mechanism, the cab and the cab mountings and every part of the body.
Our drivers could only drive for a few hours at a time because it physically would wear you out driving through a Belgium block course.
The toughest test of all, the twist course.
Imagine the terrific stress upon every fiber of the truck's structure as it surges back and forth, always under full load.
There's strain on the frame, the steering mechanism, the springs, every chassis part, the cab, hood and grill.
Every truck was different because of the wheelbase, how it would twist.
And sometimes when they build it too rigid, it would break.
[Music] [crash sound effects] Back when we were building Scouts and Travelalls, we had to crash them.
Yeah.
We had a barrier out at the track where they, we wouldnt drive them into it.
[laughter] We, they put them on We had one guy.
on a dolly that.. [laughter] They put all the way on a dolly that.. we had a dummy didnt we?
We had dummies in them, but we had a dolly, they'd put it on and it would run it into the crash barrier at a certain speed and they had all kinds of high speed cameras taking pictures.
[rock music] Once a truck model has been designed, engineered and tested, only then was it ready for mass production.
The factory assembly line is where designs become reality.
At the Fort Wayne Works, heavy duty trucks were assembled on a massive factory floor the length of four football fields.
It was quite an operation far as you could see, is the line of trucks coming down the assembly line.
That was almost intimidating to say the least.
It run almost the full length of the building.
I always like to get inside a factory.
You're seeing the birth of a truck.
Some people, you know, it's just a truck.
You just put it together.
I don't see it that way.
That is a birth of a piece of equipment that is put assembled together.
And how it all happens is still amazing that you get to drive that thing off the end of the line and starts most of the time.
The factory floor was where the main truck assembly took place.
Some parts, like axles and tires, were fed up from a sublevel.
Cabs were pre-assembled and fed down the line by the overhead conveyor.
The Fort Wayne Works had the capacity and work force to produce over 200 heavy duty trucks per day.
This was accomplished by running two assembly lines simultaneously for two shifts per day.
A separate factory was added in 1960 for the production of the new Scout in Fort Wayne.
Even though the end products from both factories were quite different, the production methods remained quite similar.
The frames came in from the outside and people started building them.
You took the frame, you added the axles.
You added all the brake lines to the chassis and everything.
And then you put on tires and you'd go from the overhead conveyor to the floor conveyor, and then you'd come in with the radiator and the engine and down the road the cab and away you go.
The front end hood and fenders and keep going.
At the end of the line it would go to a station called Roll Test.
We would put the vehicle on a rolling road and the vehicle would be tested in two-wheel-drive and four-wheel-drive.
It would be run a certain amount of time on the rolling road and make sure everything worked properly.
And then it would go to a final inspection where somebody would go through and look at the mechanicals, but make sure the doors were hung right, the mirrors were on properly.
There's no big paint flaws or a grille wasn't put on upside down or things like that.
While all of these different parts were being assembled, the entire line was on a conveyor system that was constantly moving.
Parts had to be placed and ready to go at each station along the way in order to keep the carefully orchestrated ballet moving, using a system that followed line set tickets.
A line set ticket as basically the build sheet for the vehicle.
They would use those to set the line of okay, they know on March 18th they're going to build so many travelers with blue interiors and 345 engines or six cylinder engines or whatever it was.
And they would have all those parts on the line at the right stations so that when that vehicle rolled down the line, that VIN number, all those parts would be there and they used the line setting tickets to set all that up.
Each assembly worker had to constantly perform with precision timing.
One truck after another, about 3 minutes apart.
You had to get your job done when it come in to the next station.
You have a certain pace you got to be on.
So if you don't if you don't do it, you then you're behind.
That line just keeps going.
You hustled.
You had to keep up with that line and it was hard work.
Surely after so much hustling, there would be a point where someone could hit the pause button and everyone could take a minute or two to catch their breath, right?
No, you never stopped the line.
And it had to be real critical to shut it down.
If that line stopped, a light would come on in Chicago.
They would know it right now and you better have a good reason.
With the line continuously moving at a relentless pace, it was possible for mistakes to happen.
A bolt could go untightened.
An unwanted option might be added or a critical step could be missed.
It was the inspector's job to make sure this kind of thing didn't go uncorrected.
That assembler had a line set ticket in about every 12 jobs, you had an inspector.
He checked those ten stations on the one before against their line set ticket, number one checks that it's built to order.
And number two, that it's built properly.
And if you'd missed something, they'd come back and you get in trouble.
[laughs] [fiddle music] By the end of 1963, over 1 million trucks had rolled off the assembly line of the Fort Wayne Works.
International had established a reputation for building reliable heavy duty trucks, and they sustained brand loyalty by getting input from their customers and letting their dealers take custom orders.
And they did very well out at it.
They made some nice stuff.
They had some beautiful products and they sold millions of them.
We were always proud to sell one of those trucks and sell it to a customer.
And yeah, they had their fair share of, you know, normal things that would go wrong with them.
But they were put together very well.
Commercial sales were the bulk of the heavy duty truck orders.
With America selling and moving more goods than ever.
Over-the-road trucking was big business.
In the 1960s and 70s.
Harvester was winning huge orders from major trucking companies.
They were Fleet Truck Company.
You had your big carriers.
You had Schneider.
You had North American.
You had Ryder, Feld, Saunders leasing.
That was the heart of International Harvester, right there.
Them guys kept the lights on at International Harverster.
Fort Wayne was the heavy duty truck plant for International and Springfield was the light duty.
The pickups, the Travelalls, that sort of thing were down there.
I get around Fort Wayne down there and I would use drool because that was the truck capital of the world and International, in my opinion, is the best truck ever built.
Fort Wayne was the heavy duty truck capital of the world simply because we were building the most heavy duty trucks.
We were producing 205 of heavy duty trucks a day.
Most any heavy duty truck plant in the world ever did.
One of the bestselling types of trucks being manufactured in Fort Wayne were C-O-Es, which stood for Cab Over Engine, also called cabovers.
We were the king of cabover engine trucks, so we had a number of different models on the road.
Four years in a row during the sixties, we were the sales leader.
Cabover is an engine that has the cab sitting on top of the engine rather than having a hood out the front.
In the sixties we were building all those cabover trucks because of the government length laws.
We had a 55 foot length law back then.
There was an overall length of the truck.
So the smaller the cab, the longer the trailer, the more things you could haul, the more money would make.
The advantage was you can pull as long a trailer as possible.
Disadvantage is theyre more uncomfortable, harder riding, more expensive to build.
Internationals reign as the cabover kings would eventually come to an end once the federal truck length laws were relaxed.
In the seventies, they finally lengthened the things out so you can have a truck with a hood out front.
And that made a big shift in production plans because you had to make more of those rather than the C-Os, which, well, finally completely died by about the year 2000.
[music] In addition to the cabover and conventional over-the-road semi-trucks, an International heavy duty truck chassis could be customized and adapted for many purposes, including dump trucks, wreckers, school busses and fire trucks.
Sometimes a business would need to have a truck custom engineered to fulfill a specific purpose.
This was a job for the Special Equipment department.
We would engineer whatever the customer wanted.
We worked on sold truck orders that was not regular production.
They wanted something on a truck that was special, and that's why we were called special equipment, different fuel tanks, different things mounted on different parts of the chassis.
It came to our group and we designed it and engineered it.
Big ones were some of the oilfield and Arabian desert models specifically built for that.
Here at Fort Wayne that was their biggest specialty was the enormous trucks built for the oilfields and a lot of them were based on the Paystar, which was our super severe duty truck.
Those trucks were special from front to rear.
Some of the chassis were exploration chassis.
They were called thumper chassis.
They would thump the ground and they would take a reading.
They had huge wheels and tires on them so they could do that.
It's like it's 80 feet long and two stories high.
Those were just incredible trucks, custom engineered, obviously.
All the styling for all the International trucks came out of this facility.
Engineers often designed and drafted parts.
But another important area of design is styling.
Styling combines elements of esthetics with function to make the truck more appealing to the end customer.
In general, the truck industry is conservative.
Of course, International probably was in many respects.
At the same time the design business is supposed to reach.
So it was always sort of tension.
What they do, they try to make manufacturable You pretty much you have to have an idea of what's reasonable when you start.
Practicality is everything.
A truck has to work.
It has to last.
You sure don't want to design anything that gets in the way of a function.
You want uh, to assist function wherever you can.
I think styling and design are critical to truck sales.
Just like engineering and testing a truck was a long, arduous process.
Styling involved a lot of trial and error as well.
You generally work on more than one project at a time, and in a year's time you've worked on 20 different things or so and you always want to see all of them succeed and really very few of them do.
Once the two-dimensional drawings for a body styling design were approved, it was time to take it to the third dimension.
There were stylists and there were sculptors, and the stylists do the pretty drawings of the trucks, and then they give those drawings to the sculpting staff.
And we just kind of interpret that into a three dimensional form.
We started with a regular full sized clay model.
They didn't do very many scale models at Harvester.
Trucks are huge, right?
I would say thousands of pounds of clay, but the clay is only maybe three inches thick.
Underneath that is a big buck we called it.
Thats made out of wood with styrofoam on the outside.
It's very easily carved.
So you can put any shape on there you want.
You can change it as many times as you want to, which happens daily.
The design changes over time.
I mean, it takes a good year or so to get this all refined.
So you're always coming in every day and tweaking.
They'll come in there and say, Well, I don't like where that line is on the side.
Can you move that a little bit?
Or the swoop and the fender doesn't look right.
Can we change that?
The goal was to make the full sized clay model look just like a real painted metal vehicle.
But the clay couldn't be painted directly.
The clay models, they would use a thing called DI-NOC, which is very close to a decal.
So I would paint that and then they put it on the vehicle.
You bring it back and you put it in water just like you would put a decal on a model airplane or something.
When that's finished, you come in and if you have chrome on the car, you take regular tinfoil and you put it right on the clay and you squeegee that on and smooth it out.
When it's finished It looks just like the vehicle that you want it to be.
Another high point in Harvester styling came with the addition of Detroit stylist Ted Ornas in the 1950s.
Ted had done a number of things, including some contract jobs for International, and he was just about ready to give up the whole business.
Things were going down the tubes and he wasn't having any kind of luck at all.
And he got a call from International that of all things they had decided to have an internal design staff and wanted him to run it.
[music] Ted Ornas is credited with the styling for one of the most significant International Harvester product lines of the 20th century.
The Scout, a lightweight, nimble, four wheel drive, all purpose vehicle, came about from desire to compete against one of the most famous names in off-road vehicles: Jeep.
The origins of the Scout start with a trip that a bunch of executives made out west.
They saw way too many Jeeps doing things that they thought International Harvester vehicles could do.
The original concept was to add a compact light truck to their light truck line.
it was going to be really cheap.
That's where the legendary Ted Ornas kitchen table design comes from.
So that vehicle that he drew in that kitchen table drawing when evening after work, he showed that around to the executives and got the first kind of smiles and positive feedback that he had gotten from the project so far.
steel body development.
It was 1958.
The design for the new all purpose vehicle finally had the green light.
To accommodate the production of the new model line, International Harvester purchased a 500,000 square foot factory from U.S. Rubber Corporation.
The former World War II production facility had been used by Studebaker for making engine parts for the B-17 Flying Fortress and was located very near to the Fort Wayne Works.
Ornas had started the styling process for Scout in 1958 and the Fort Wayne Works engineers were able to make the Scout factory ready in only two years.
The first Scout rolled off the assembly line on December 1st, 1960.
Vehicles bearing the Scout name arrived at International Harvester dealers as early as 1961.
The public received the new vehicles with open arms.
Orders quickly outpaced production despite building over 28,000 in 1961.
Scouts were backordered pretty much for the first year.
They were always behind that first year order versus production.
Scout was an unexpected phenomena to International.
One factor that led to the success of the Scout was its widespread appeal.
Due to the variety of uses and multiple configurations, it was able to span the gap between work utility and sport utility vehicle.
Farmers and businesses found it well suited as a rugged work vehicle, but it could also be used for camping, fishing and exploring.
What's more, it could be used as an everyday personal vehicle as well.
It's a bunch of things.
It's an off road vehicle.
It's a suburban grocery getter.
It's a race truck.
It's so many different things and so flexible.
Even on our first brochure for the Scout, we show like five different configurations.
It's just an incredibly distinctive product that's known all over the world.
I tell people who I work for, I say Navistar, and nobody knows who Navistar is.
I say, Oh, it's the old International Harvester Company.
And right away they know two names.
They know Farmall tractors and they know the Scout.
It's incredible, the following.
[music] The Scout was opening doors to new customer bases that International Harvester hadn't tapped into before: recreational users and suburban families.
They were transitioning from a purely commercial vehicle, which was what it was originally intended to be, to a kind of a mass market or civilian vehicle, if you want to use that term, where people used it maybe as a second car, but certainly as a recreational vehicle.
Most people couldn't afford to own a vehicle that would just go playing in the mud The accommodations of the first Scout built in 1961 were indeed Spartan.
This first generation was called the Scout 80.
At the time it came out, it was a few steps ahead of the Jeep in the short wheelbase utility vehicle market.
It was more comfortable, more weather tight.
and they had a little bit more style.
They weren't as boxy.
The original Scout was configured to be built in three different ways.
You could have a roadster, you didn't have doors, you didn't have a top.
They had a fold down windshield.
The base configuration, though, for a Scout was what they called a cab top.
A cab top was a pickup.
Basically.
It had a removable top.
It had a fixed bulkhead behind the seats.
You know a pickup, you have to have some way to divide the passenger compartment from the cargo compartment.
Right?
The third configuration was what they call the travel top originally, just the means to cover the load area.
They fooled around with some ideas to put rear seats back there, but they realized that wasn't going to cut it.
They need to make a station wagon out of the Scout because their original picture for the Scout was a light pickup and they thought that the market was going to buy a lot of two wheel drive versions of it.
Well, people were ordering four wheel drives with the travel top, which was their name for the full length top.
They had to scramble and redesign the body so that it would have what they called a walk through feature.
Could be configured as a station wagon or as a pickup.
All the tops were removable, so if you bought a cab top, you could easily change it out for whatever.
In 1963, the Fort Wayne Works reached a milestone of producing 1 million trucks over a 40 year time span.
In 1964, the Scout reached the 100,000 mark after only three full years of production.
[music] [swanky music] The Styling Department was given the task of making the Scout more upscale by revamping the interiors with posh features and adding a bit of bling to the external appearance.
63, there was a lot of big changes in the Scout 80 that moved it up the comfort food chain.
And then in 1964, they took a giant leap with the Red Carpet series Scout.
That was the first time the Scout had been offered with anything close to comfort and style.
When the Scout first come out, there wasn't anything like it on the market and was bought up by a lot of women, had their say in owning a Scout.
I sold Scouts to women, too, that thoroughly enjoyed them, and that's what they wanted.
While the vehicle certainly appealed to the general public, it wasn't always sold at a place the average person would go to to shop for a family car.
International Harvester sold most of their stuff out of either truck dealers or farm equipment dealers.
You had to go to a farm equipment dealer to look at a Scout.
You had to go to a truck dealer to look at a Scout.
That would really, really hinder them the whole way through the production of the Scout.
[engine accelerating] Even though the customer had to go the extra mile to find a Scout dealer, the demand for the Scout remained strong.
International Harvester responded to the shift in buyer demographics by introducing the new and improved Scout 800 to the masses in 1966.
They needed to tame the Scout down, turn it into less of a commercial vehicle and more of a mass market or consumer vehicle.
That's primarily what they addressed with the 800 was making it more comfortable, more quiet, more stylish.
1966 was a record breaking year for the International Harvester Truck Division, producing over 175,000 trucks in the U.S.A.
The ever increasing Scout production helped to push the Fort Wayne Works to a new record with 65,999 total vehicles.
International Harvester updated its operations in Springfield, Ohio, with the opening of a brand new factory with more capacity to produce pickups, Travelalls, and medium duty trucks.
1966 also brought some heavyweight competition into the ring against the Scout.
The Ford Motor Company rolled out their new SUV, the Bronco.
The Bronco immediately took a big chunk of their market share.
I mean, they were doing okay prior to that.
They were selling really well against the Jeep.
But then the Bronco came along and, of course, Ford Motor Company, they could build more vehicles in a day than International could build in a year.
The Fort Wayne Works engineers were working diligently to modify the Scout 800.
Meanwhile, Chevrolet jumped into the SUV market with the Blazer in 1969.
Once again, this put pressure on International Harvester to step up its game to stay in the competition.
The answer was the Scout II, introduced in 1971.
The 800 line was lagging behind the rest of the competition and the Scout II put it right on an even keel with everything out there.
Not only did they have a larger, more stylish body that had a lot more room in it, it was easier to get in and out of.
It was much quieter.
It was much safer.
It was much more capable of being a second car than the previous generation.
Plus, they had powertrain parity with everybody.
being able to haul more, go faster.
They'd never had air conditioning in the Scout prior to the Scout II.
They didn't have power steering in the Scout prior to the Scout II.
The improvements introduced in the Scout II gave the SUV an even broader appeal.
Collectors like Sam Elliott still seek out restore and drive this iconic vehicle more than 50 years after its introduction.
The Scout II, disc Brakes and power steering.
It was so much easier to drive and just a better truck.
after you have a Scout II it's hard to go back to a regular old Scout.
It was a big jump ahead for them and it put them on equal footing with basically everybody building SUVs at that moment in time.
[music] It wasn't long before the competition on the sales floors spilled over onto the dirt roads of the desert.
Four wheel drive enthusiasts wanted to see how their vehicles stacked up against their rivals.
That spirit of competition spawned one of the most extreme endurance races known to man.
It's an intense thing.
If you're running the Baja 1000.
It's a week of grueling punishment.
Out West when they had Baja, That was blood.
They were after money.
The first of these desert racing warriors to drive a Scout in the Baja 1000 and win was Jimmy Jones in 1972, It wasn't just the pros that were having all the fun.
Four wheel racing clubs were popular all across the nation.
The Fort Wayne Works guys put together a team to show their Scout pride.
We formed a club, the Fort Wayne Four Wheel Drive Club.
We bought one of the in fact, it was one of the pre-production mock ups that was used in development.
And they were done with that, bought that and built it into a racer.
And we started racing with that one first.
And then a couple of others were built over the years after that.
Even in the stock class, they were the ones to beat.
We were still in stock class with the allowed modifications we had, but we'd upgrade so three people could drive it in a racing weekend.
And we often were competitive in every class.
I got to meet some of the guys that did it and it was the hot dog, beer-drinking fun time and they werent they were competitive because they're racing Jeeps, but these guys were doing it for fun just to kick dirt in that guy's face.
The Scout was well suited for the racing environment because we could do quite well compared to most other people.
And having a having a couple of engine engineers involved.
We had a real well-running engine and we were competitive with most of the rest of the Jeeps and Broncos and everything else.
[rock music] The Scouts stepped into the world spotlight in 1976 when International supplied the U.S. Olympic ski team with their official vehicles for the Winter Olympics in Innsbruck, Austria.
This was also the year for the bicentennial of the United States.
It was a good opportunity to show the American flag and get International involved in the Olympics.
So they developed a bicentennial-themed Scout for the Olympic team, and they built 17 of them.
They were 76 model years, but they were built in 75.
In 1975, the US was facing a recession that was coupled with fuel shortages caused by an OPEC oil embargo.
Gas prices skyrocketed and Americans were looking for more fuel-efficient vehicles.
This contributed to Harvesters decision to discontinue its light line of gas-guzzling Travelalls and pickup trucks being made in Springfield; some of the medium duty truck production was transferred away from Fort Wayne to take advantage of the excess capacity in the newer Ohio factory.
Although International Harvester was a public corporation, its top management seemed more like a family business run by successive generations of McCormicks through most of the 20th century.
In 1977 CEO Brooks McCormick, the great-grandnephew of Cyrus McCormick, decided the company needed fresh thinking leadership to propel the company forward.
In 1977, Harvester hired Archie McCardell away from Xerox to come to Chicago and to run the company.
Brooks McCormick recognized big changes had to be made.
I don't think he had the heart to do them, which is why he resigned.
And they brought in Archie McCardell given instructions to make some changes.
He was paid the sum of $460,000 a year and given a $1.5 million signing bonus.
This was unheard of money back then and made him among the few highest paid public company executives in the United States.
This fact was not lost on the rank and file and the UAW when contract time came around.
Two years later, McCardell started by having International Harvester department heads identify ways to make cost-saving changes to their budgets.
This resulted in an increase in corporate profitability in 1979.
Employment at Fort Wayne is at a record-high 10,500.
The stage was set for a battle when McCardell turned his cost-cutting scissors to one of the companys largest expenditures the labor contract with the UAW.
Theyd always had a tenuous relationship with the company.
On August 9th of 1979, Archie McCardell and Hank Crandall, his second in command at the time, met with Pat Greathouse from the UAW to start working on the new contract.
I think the board had full knowledge of what they were going to demand.
You know, they wanted to get some concessions from the union.
Union wasn't going to do it.
So the two heads butted.
It didn't take long for negotiations to break down.
In fact, they hardly got started when a week later, on August 12th, it was announced that they'd had the best quarter that they'd had in years and the highest profit they'd had in years.
And here they were demanding quite a number of concessions from the workers, and it just didn't fit together.
He had some justification in wanting to negotiate better terms with the UAW, and that was probably a good idea as far as, you know, saving the company or at least bleeding a little less red ink.
But his timing was horrible.
It was a game of chicken and neither side blinked.
Negotiations between labor and management historically have involved some level of brinkmanship.
Eventually, demands and differences are mediated down to an agreement consisting of compromises from both sides.
This time however, Harvester and the UAW were so far apart on their demands that both sides ended up walking away from the bargaining table.
We met two full days, Tuesday and Wednesday, and the company failed to resolve any of the local issues or a single grievance.
The company left Thursday morning stating there would be no more meetings.
The news of a possible strike went out Thursday afternoon to Fort Wayne Harvester workers from UAW Local 57.
A walkout would idle 8000 of the 10,000 workers here.
The remaining 2000 are nonunion personnel, and they would be expected to report to work.
The UAW was in no mood to bend to the demands of Archie McCardell and Company.
On November 1st of 1979, they went out on strike.
They walked out at noon.
Minutes after workers filed out of the Harvester plant, picket signs were up.
‘course, all these guys got out, dropped their lunch boxes out there and started a picket line right there in front of that main gate between the tower and the branch building.
Well, unbelievably, it was an executive there on so-called mahogany row.
And and hed come up to me.
‘Jim, you got all this union relations background.
You got more than anybody.
Go out down there and break up that line.
I said, ‘They have a legal right to picket.
There's nothing wrong with it.
They're totally legal.
The specific details of a contract negotiation were always kept private until it could be presented to the entire UAW membership for ratification.
Some issues were known but others could only be speculated on.
But the unions out there and they knew of a couple of issues.
Let's say three issues.
They didn't know the top ten issues.
They didn't know the other 47 issues.
So they're out there blind wondering why they're on strike.
Management, I'm talking foremen, all the way to the top, did not know why we let them go on strike.
Management did not know what the company was after.
When contract negotiations stalled, UAW members directed their anger toward one person, Archie McCardell.
That sentiment still lingers more than 45 years after the strike.
What do you think was the reason for the breakdown in negotiations?
Well, I think it was the main fault was Archie McCardell.
He wanted to break the union.
He was like a hatchet man.
The board said they wanted to take care of the UAW, get rid of them.
My thought he was the downfall of the lot, but the economy and everything else also entered into that also.
During 1980, we were having the recession, which many economists felt was the worst recession since after World War Two.
Interest rates were 17%, unemployment was 10.9%, They took out massive bank loans to keep the cash flow going, and it was the beginning of the end for the company As Harvester braced itself to weather the economic storm, UAW workers in Fort Wayne piled up firewood, hoping to keep warm in the long winter months during the strike, well aware, they, too, were in the same economic storm without their main source of income.
If you hadn't prepared for it, you were going to be in trouble financially.
At the local 57 union hall, members were now signing up for picket duty.
Sign it right here.
Bring that card back when you walk, picket and to collect your benefits check.
We had to walk the picket line.
They give certain days, you know, we had to come up and do it.
It was cold, wintery, and just kept warm.
It's not a good feeling because you don't know when you're going back.
The only one got hurt was the company because the union, you know, they stood together and fought them hard, you know, for what they believed in.
We wouldn't break.
They would be on strike for 172 days, just shy of a little over six months.
I was glad when it was over.
The strike ended on April 20, 1980, after UAW members ratified the new contract.
The strike had depleted the savings of many workers and the company had sunken deeper into debt.
Over the next six years, International Harvester would post consecutive annual losses totaling $3.4 billion.
The big thing was it brought to light the shortage of capital.
The strike ended because International Harvester was out of money.
A lot of people want to say it was Archies fault.
I think he was, he was brought in to try to save a sinking ship and couldn't quite do it.
[music] That sinking feeling persisted into the next decade.
By 1980, International Harvester was besieged with difficulties on every side.
The company was still limping from the effects of the prolonged strike.
The US economy was in a recession and sagging sales of the Scout line due to these external factors were making it look more like a liability than an asset to the top brass in Chicago.
The gas crunch had really hurt.
That hurt the entire auto industry, cut into their profits because they had to adapt to fuel economy standards.
They had to adapt to an emission standard.
They didn't renew the emission certification for the Scout.
Emissions testing is so expensive because engine testing and development is so expensive.
And so if you have to come out with a new engine to meet the regulation, the emissions regulation, it's expensive and you need to have a lot of volume to spread that expense.
We didn't have the volume of engines to amortize the cost of all the development work for that.
We went on for a few years, but again, it got to the practical realization that if you're not building thousands of them a day, only hundreds a day, it gets very difficult to sustain that continuing compliance cost.
Harvester was drowning in debt and desperately in need of cash.
Perhaps if they could get someone to buy the Scout line instead of ending production, it would be a win-win.
They needed a hero to ride in on a white horse and save the day.
Ed Russell was an entrepreneur.
He came from the Midwest.
There's nothing more Texas than a midwesterner that transplants himself to Texas.
He had the big cowboy hats, boots, the shirts, the whole bit.
Russell had built But while the strike was going on, I don't know exactly what was happening behind the scenes, but they decided to offer the Scout division up for sale, that maybe somebody would buy it.
And I don't know whether they had Ed Russell in mind from the get go or he was just the first person to stand up and say, you know, I'm interested.
So he put together a consortium of people from the Fort Wayne area and allegedly Steyr-Puch in Austria was going to be involved in it.
And they were going to buy the Scout name.
They were going to lease the factory.
On October 8th, International Harvester announced they were terminating their agreement with the Texas investor due to a failure of certifying financing.
And as a result, it would cease production of the Scout line on October 21st.
Workers had only a couple of weeks before their jobs would end.
It was just moving ahead and boom, the end.
[ominous music] Several factors appear to have been involved in the decision, but perhaps the biggest was International Harvesters corporate financial problems.
The company was out of money.
The projects we had in spring of 1980 were ranked and the most profitable ones were chosen.
There was enough money to do the first two projects, and the Scout came in number three.
I don't think the company wanted to save the Scout.
I don't think International Harvester really wanted it.
There were elements within the Scout division that certainly wanted to save Scout, and I think they had a pretty good business plan with the save Scout, and I think that business plan wouldve worked.
But I think International Harvester made up their minds pretty early on that they wanted to end the Scout.
The decision culminated with the final Scout rolling off the factory floor on October 21st, 1980.
There was no cheering or hooting and hollering.
Everybody was their chin was down and there was no tears.
But it was a very emotional day.
It was very, very sad day.
It just brings tears to your eyes.
I mean, not just the pride, but people losing their jobs.
I think the number was 464, if I recall correctly, that lost their jobs as a direct result of the Scout going away.
When I got five years in, I figured I had a job for life, but the economy and the way things went and company...
When all was said and done.
532,674 Scouts had been produced in Fort Wayne from 1960 through 1980.
The story came full circle in 2023 at a Harvester Homecoming event in Fort Wayne, when the freshly restored first Scout produced was displayed side by side with the last Scout to roll off the assembly line.
[upbeat funk rock music] The Scout remains a highly collectible vehicle all over the world.
Even today, more than 40 years after the last one was made, Scout enthusiasts gather at a variety of events like this one in Fort Wayne to display their restored vehicles, swap stories, and celebrate the Scout.
And a lot of it is the people, the people that own them.
I put on a show and go to shows across the country and talk to the owners, and it's kind of a family.
A lot of people know me by that truck.
They might not be all fancy and smooth riding, but it is built rugged to take the punishment.
I love the vehicle.
I started collecting Scouts in early seventies.
The first one was a 61, and it wasn't fast, but it was a lot of fun When the roads were bad, you get down the road with it in four wheel drive.
You can get anywhere you want in bad weather and that Scout had saved our lives a couple times.
In the winter we pull the sled behind it.
In 1978, I ordered a brand new Scout, and my name was on the windshield when it went down the line.
I had two Scouts of my own.
The first one in 72, I walked the line with it while it was built.
I've owned three Scouts.
How many do I have?
How many of you owned over the whole... Oh, my gosh.
I thought I counted 27 or 8.
Another thing that makes the Scout so collectible is the relatively small number of units produced.
They're rare.
You only built 550,000 of those.
So, for example, a 69 Camaro is something I used to be into.
Well, they built 500,000 of those in one year.
It brings me back to a younger George Kirkham.
A little bit of a young, impressionable salesman and it's a history lesson.
Driving them every day, every time I get in one, it's a history lesson.
Yes.
They're not as refined as your modern day Suburban or whatever that I drive.
But that's the way things were back then.
[music] [melancholy music] Terminating the Scout line in 1980, barely moved the needle in terms of bringing Harvester back towards profitability.
Even though its truck sales worldwide were a hefty 3.3 billion dollars the truck division barely managed to break even with expenses.
Internationals flagship agricultural equipment group reported a 30 million dollar loss and the struggling construction equipment business posted a 23 million dollar loss.
We continue to make more and more sales and we continue to make less and less profit.
Our sales were good and our profits were terrible.
In December of 1981, Archie McCardell and the board were able to work out a deal with the companys nearly 200 creditors to restructure its crushing 4.2 Billion dollars of debt.
This refinancing deal was seen as a temporary reprieve to keep the industrial giant from filing for bankruptcy.
Back at the Fort Wayne works, only 5,000 employees remained on the job compared to the 10,500 workers employed before the strike.
The city of Fort Wayne was suffering, with a jobless rate of 11%.
1982 would also be Archie McCardells second contract negotiations with the UAW.
His argument for 100 million dollars in concessions from the union, seemed stronger than ever against the grim economic backdrop.
At this point it was looking like the future of the entire company was in doubt.
Perhaps it was this realization that their very livelihoods were at stake, that brought the UAW back to the bargaining table.
The average union employee made $12.35 an hour, compared to a minimum wage of $3.35 at the time.
A deepening recession was keeping unemployment levels in double digits.
It was no time to be on strike or much worse looking for work.
Times were tough.
You couldn't get a job at Ford Motor Company, Chrysler or GM.
Everybody was laid off.
McCardell and Harvester had the upper hand this time.
On May 2nd, 1982, UAW members ratified a new 29-month contract that included an astounding 200 million dollars in contract concessions.
The next day, it was announced that Archie McCardell and International Harvester were parting ways.
Louis Menk replaced him as chairman of the board and Don Lennox became the new president and chief operating officer.
Back in March, Harvester had sent telegrams to the government leadership in both Fort Wayne and Springfield asking the cities to put together aid packages to help keep the manufacturing facilities in their towns open.
I'm Karl Bandemer.
I was the economic development director under Mayor Win Moses.
When Harvester announced that it was liable to leave, that that really elevated the concern.
The mayors office held meetings with the local Harvester executives to assess what they could do to retain Fort Waynes largest employer.
Clearly, Harvesters main needs are cold cash that there's very little in the way of of deferred obligations or guaranteed loans that are going to be of significant benefit to them.
City, county and state officials went to Chicago this morning to talk with officials of International Harvester about a financial assistance proposal to keep this plant afloat.
When the government delegation returned from their meeting with Harvester executives.
A press conference was held outside of the factory to reveal details of the 20 million dollar incentive package.
All seemed to be going well until International Harvester made a bombshell announcement on July 29th 1982.
The company would be consolidating its truck manufacturing facilities from 3 factories in North America to just two.
The three factories involved were Chatham Ontario, Springfield Ohio, and Fort Wayne Indiana.
It soon became apparent that the Canadian facility would remain open.
This meant either Springfield or Fort Wayne would have to close.
Fort Wayne was now in a fight to keep their crown as Heavy Duty Truck Capital of the World.
I truly believe they have not made up their mind.
Mr. Dean Stanley, who's head of engineering group, talked to Mr. Menk,and he point blank asked them, Are you going to close Fort Wayne?
And his response was, It's an option.
That kind of set this whole competition in motion.” We knew that we were going to have to step up and figure out how we were going to influence Harvesters decision.
Fort Wayne Mayor Win Moses spearheaded the effort to convince those in state and county government and the local business community that giving public assistance to a private company was in everyones best interest.
Given the number of of Harvester employees here.
If they were out of a job, that means they weren't going to be able to shop in your stores.
Chances are they weren't being made their mortgage payment.
There was going to be a huge impact beyond just the fact that Harvester might shut down.
So you need to get on board here and, you know, work with us to try to save Harvester and keep them here in the city.
The Fort Wayne community responded to the cause by making pleas to state officials, holding rallies downtown, and filling sandbags with letters to show their support for keeping Harvester jobs in the city.
Community and state leaders in Springfield Ohio were working just as hard to convince Harvester to stay in their community.
The two communities locked in a contest for survival caught the attention of struggling Americans everywhere.
This competition got national attention.
It was front page on The New York Times , The Wall Street Journal .
This morning, Harvester employees in Fort Wayne, Indiana, went to work wondering whether theirs will be that one.
In the past two years, these men who make trucks have watched their assembly line shrink from 10000 to 4000 workers.
Harvester used to be the number one employer in Fort Wayne.
This big old building used to be a place you could rely on.
Used to come in and figure, Hey, you was going to stay here and here.
Probably get your time in.
If you live to be 65, you could retire.
But now you just come in, figure maybe you'll get through the day.
Maybe you'll get sent home at noon.
We'd just like to know whether we've got a job or whether we don't.
It'd be terrible if we don't have, but the dread of not knowing is even worse than knowing.
You really didn't know where corporate was.
They said they didn't have a preference, it was just going to be who's going to put together the best package.
Offers were presented to the top management at International Corporate headquarters behind closed doors in Chicago.
Governor Robert Orr and Lt.
Governor John Mutz represented the Indiana state government.
The bankers were heavily involved.
At that point they were helping us save the company.
And I understand they toured both Springfield and Fort Wayne.
Springfield Plant was much newer than the Fort Wayne facility, so that was probably a strike against us.
On the other hand, it was our understanding that the productivity in Fort Wayne was much better than the productivity in in Springfield.
So that was to our advantage.
Both cities were constantly working to meet or exceed what the other was offering Harvester in a high-stakes game of one-upmanship.
We're always trying to figure out exactly what the other party was trying to do so we could hopefully match them or trump them.
The nearly nonstop effort to bolster Indiana's Harvester aid package continues here at City Hall.
And with today's news that Ohio's $30 million of aid is set to go, the pressure is mounting.
I think we're on borrowed time right now.
As soon as Ohio's package was completed this morning and that the state will have to finalize their proposal very quickly here.
The states addition to the incentive package will be about $4 million.
Additionally, Fort Wayne's five banks have added approximately $8 million, bringing the Indiana total to about $32 million.
The Ohio package stands at 30 million.
With summer fading into fall.
It seemed optimism was fading in Fort Wayne as well.
Local Harvester workers and city officials were originally told the decision would be made in a few weeks.
The waiting had now dragged on for nearly 2 months.
Just leave.
We don't care anymore.
I don't think we can say that.
You know, maybe, maybe in the mid-sixties, when the economy was booming and you could find other employers easily, you could say that.
I think we've got to fight as hard as we can and as long as we can to keep what we've got.
The anticipation was palpable as rumors spread that International Harvester may be close to a decision.
Can you say that tomorrow morning, International Harvester will hold a news conference to announce they are moving to Springfield?
No, but I would not be surprised if tomorrow or Monday they would.
They would hold such a news conference to to announce their decision.
The decision is imminent and the decision will be unfavorable.
They're going to shut down Fort Wayne.
The announcement that everyone anticipated and dreaded came on September 27, 1982. International Harvester will phase out truck manufacturing in Fort Wayne, Indiana.
This decision comes as a harsh blow to thousands of individuals who work for this major employer.
I am not surprised.
I am disappointed.
Harvester President Lennox said he was impressed with Fort Wayne's multimillion dollar incentive package, but added money was not the deciding issue.
The overwhelming advantage was the fact that the Springfield plant is a much newer, much more cost effective plant.
I guess theyre doing the best for the company.
I don't know.
I think they knew what they had planned all the time.
Naturally a little sad about it.
But, you get, you have a few sad moments in your life, you know, and you just got to regroup and go back on.
It was heartbreaking.
It really was To see that happen again.
Oh, broke my heart.
That was a big thing to me.
Going to Fort Wayne.
Seeing all them trucks.
This tale of two cities had ended with a winner and a loser; rejoicing and mourning.
When Springfield was picked, everybody was really happy.
I wish when they voted, they voted to keep Fort Wayne.
Some of the long time employees are hoping Harvester will hang on long enough for them to retire In only a matter of months, over two thousand Harvester truck factory workers would soon join the ranks of the unemployed.
With the decision finally made, Fort Wayne workers were at least able to start preparing for the next phase of their careers.
The good news is that most of them would have several more months of employment to count on.
About 200 factory workers would be laid off in November.
Another 800 will be gone by next summer.
Harvester representatives in Chicago told News 15 about 1900 local workers will not be affected by the phase out.
Those not affected divisions are the axle and transmission plant, the materials management plant, the worldwide truck engineering center and the parts distribution center.
The illusion of job security for those departments “not affected,” would soon be shattered as Harvester continued to make more cuts in the months that followed.
December 1st, 1982: Harvester announces it will cease making axles and transmissions at its Fort Wayne Works 500 jobs are eliminated.
April 20th, 1983: Harvester announces it will close the Fort Wayne Material Management Center.
200 more jobs are eliminated.
Then in July of 1983, a 60 year run came to a halt as the last heavy duty truck made its way down.
The assembly line at the Fort Wayne Works.
As the 1,527,299th Harvester truck rolled off Fort Wayne's assembly line.
The reality of the shutdown hit home when the line was stopped and their tools set aside.
Employees knew it would be for the last time.
[indistinct chatter] its all over.
[Whistle blows] I'll never forget it was July the 15th, 1983, and it was a really very sad day when the whistle blew for the last time.
That was very sad.
It was very painful.
That whistle didn't blow anymore.
This would be the final day at the Fort Wayne Works for 1700 employees.
We got laid off.
That was a big layoff.
I was laid off for four years.
I got laid off for six and a half years and the big cutback happened.
Nine hundred employees at the Engineering Center and the Parts Distribution Center were not affected by the plant closure and would keep their jobs in Fort Wayne.
[timeclock punch] The five hundred remaining factory workers with seniority would be able to stay on to assist with the dismantling and sale of the plant's equipment but all of those jobs would end by November.
They were taking out all the machinery out and everything was going out.
I mean, you begin to see what was really was happening when the floors would begin to look pretty empty.
450 is here, 500 now, five, five and a half, six hundred dollars [indistinct] Once the factory was completely shut down and the last tools and industrial equipment had been auctioned off, it was decision time for some of the workers with the most seniority.
Join the thousands of Fort Wayne job seekers in the unemployment lines or transfer to the Springfield, Ohio, factory.
In November, they sent a lot to office people to Springfield that was on the list.
And so they got to my seniority and I was transferred to Springfield in November of 82.
[music] Union workers from Fort Wayne had the option to “bump” a lower seniority worker off the Springfield line.
This was crucially important for the ones that were close to retirement age who wanted to lock in their pensions.
The drawback was, they would either have to relocate, or make the 250 mile roundtrip commute from Fort Wayne to Springfield.
You had to go by seniority.
And so actually, there was a waiting list to get in there.
Finally, I was able to go back to work in Springfield.
A lot of the guys that had 20 years, they had to go down and finish.
They had to go down there.
Many of my friends chose not to go to Springfield, Ohio, due to families and roots and, you know, homes and such.
I was lucky enough.
I got called to Springfield in February of 84 and I'd been laid off in July of 83.
That was an exciting time, you know, for us.
It was a time that you would realize that it was nice to get back to your job because you're sure seniority would continue and you were able to retire when you got your time.
In fact, I spent about 19 years after I left Fort Wayne in the Springfield area.
A lot of them went there mainly to get there 30 years and then came back.
I was there for 20 years and I went back and forth on weekends and lived there during the week.
The bus ran every day.
And there was a gentleman that had the bus, owned it.
He was from Angola, so he would drive from Angola to Springfield, Ohio, with the bus every day.
And so that went on for easy 15 years.
Four buses that held about 40 people each, that made the trip to Springfield every day and took workers to work two and a half hour drive each direction.
They had to get up like 3:00 in the morning and get home at 7:00 at night.
I rented a place.
It was really too far to drive back and forth.
Some drove a car with maybe two or three passengers, but only time I would come home would be on a Friday night, for Saturday and Sunday.
There was a lot of guys that moved down to Springfield.
There was a lot of guys that moved down to Springfield.
There was a place, a trailer court in there that it was called Little Fort Wayne, and a lot of the guys bought trailers, or rented the trailers there.
It was like a little city of people from Harvester.
They used to work there.
My uncle did that for years down there, and he ended up in a trailer, him with three or four other guys living in a trailer, and then they would come back on the weekend.
But, Fort Wayne was such a center of their lives.
They had kids in high school.
They didn't want to leave Fort Wayne.
Which under the circumstances it wasn't the best situation because a lot of the people that used to work for for Fort Wayne actually had more seniority than a lot of people in in Springfield.
So there was some situations that you found yourself sometimes, you know, at odds with some of the Springfield people and then really didn't care too much for us from Fort Wayne.
It was kind of radical at first in a lot of people in the factory had problems with flat tires and and didn't like the people there because they took away their jobs, you know, because of seniority.
Any time somebody comes in and what they call bump you off the line, they might have seniority from Fort Wayne and they come and take your job and you have to go do a lesser job, which is a union thing, so.
But eventually, I think it began to the place where after a time it begins to settle down and then things begin to work a lot better.
Met a lot of good friends there in Springfield and a lot of people became friends.
I mean, it it worked out good in the end.
I know a lot of people that moved over here from Fort Wayne and theyre just good people, just like Springfield people.
[sad delta blues music] Not everyone had jobs waiting for them in Springfield through no fault of their own.
They had been severed from the only job they had ever known.
I see no way that we are going to bring this community back during the entire decade of the 1980s to anything resembling the level it was in the 1970s.
It was a blow to us.
I mean, it was a it was a disappointment.
But I think in many respects, it kind of hardened our our economic development efforts.
I'm not in any way pessimistic about the city and the future of our community.
We've learned something this past year about this city and about our people.
No matter what confronts us.
We band together.
We muster our resources and come out ahead in the long run.
Even though the city was facing a grim economic forecast.
Mayor Win Moses and his team acted quickly to preserve the hard earned economic development funds previously offered to Harvester.
Shortly after the announcement that the Fort Wayne works would close, Karl Bandemer made a request to the City Council.
I asked Council to keep in place the funds that they had that that we had come up with locally for ah for an economic development effort.
And I believe that the vote was unanimous.
With the incentive funds secure, Fort Wayne was able to get the attention of a major employer with a huge potential project.
I got a phone call when I was on vacation from the mayor and said I had to be in Indianapolis the next day.
So I went down, we met in the governor's office.
The county was there, other people from the city were there, people from the state, and the people from General Motors were there also.
General Motors was looking for a location to build a new factory for the manufacture of full-size pickup trucks.
They presented the state and local representatives with a list of conditions to meet in order to secure the deal for Fort Wayne.
This would require an effort very similar to what the city had done to win the International truck factory back in the 1920s.
On August 31, 1984, just a little over a year after heavy duty truck production stopped at Harvester, General Motors announced it was going to build a 2.5 million square foot truck factory in Fort Wayne.
The new plant would employ 3000 workers with an annual payroll of over 100 million dollars flowing into the local economy.
Sixty three years after the first truck was assembled at the new International Harvester factory in Fort Wayne.
The first pickup rolled off the assembly line of the new GM plant on December 8th 1986 ensuring that Fort Wayne would remain a “Truck Town for decades to come.
[music] Even before the GM plant was announced, there were still men and women working at the International Harvester Engineering Center in Fort Wayne.
They had been spared from disaster, much like how one house remains intact after a tornado, while the house next door is completely demolished.
The storm was still swirling around International headquarters in Chicago.
In November 1984, International Harvester Chairman Don Lennox announced the company had made the “monumental” decision to sell the agricultural equipment division.
The deal with Tenneco, the maker of Case equipment, would give Harvester 430 million dollars, allowing it to pay off a good portion of its long term debt.
When we sold off the Ag business.
Finally in 84, we were probably hours away from bankruptcy.
The agreement with Tenneco also included the transfer of the “Harvester” brand name along with the farming equipment business.
This resulted in the corporation changing its name in 1986.
The company would now be called Navistar, and the main product line would still be branded as “International” trucks.
Workers in Springfield and Fort Wayne would now have a new name on their paychecks.
When I started, it was International Harvester.
My first paycheck was the International Harvester.
But then very quickly changed to Navistar.
But a lot of people didn't realize, even in Fort Wayne, that this engineering center was still around.
Not only was the same kind of engineering design and testing being done at the Truck Development and Technology center, but the proving grounds remained in operation as well.
The newly rebranded Navistar had emerged on the other side of the storm, a leaner, if not stronger, organization.
The corporation had gone from 47 manufacturing facilities in 1980 down to just 8 plants in 1986. we were starting to bring people back.
there was people who were laid off with less than 20 years experience that were starting to get rehired.
Many engineers were able to come back and work long careers for Navistar in Fort Wayne.
The engineering and design job stayed until 2012, when operations were moved to Navistar headquarters in Lisle, Illinois.
Fourteen hundred jobs were affected and only 300 employees accepted offers to transfer out of state.
It had been 29 years since the last truck was assembled in Fort Wayne, but there were still important work being done here during those years.
The proving grounds continued to test trucks, it would be another five years before the last International truck made the final lap around the track in 2015.
Operations were transferred to a larger facility built by Studebaker near South Bend, in New Carlisle, Indiana.
After all was said and done, International trucks had a total run of 92 years in Fort Wayne.
Harvester had said goodbye to the city, but this “Truck Town” wasnt quite ready to say goodbye to the trucks that were made here.
[music] [music] Those who had worked here in Fort Wayne felt like the legacy wasnt being preserved.
Many of the current residents werent aware of the history that had taken place here over the last 100 years.
Something had to be done before the memories had faded away.
In 2019 a small group of individuals started planning a reunion of sorts, to bring those memories back to the attention of the Fort Wayne community.
Harvester Homecoming is really the brainchild of Ryan DuVall.
He said, I'd like to do something to help restore International Harvester and the history here in Fort Wayne, because nobody was doing that.
In June of 2019, planning for a Harvester Homecoming event was underway.
The group began contacting former employees, Scout collectors, and big truck enthusiasts to bring their vehicles to the event.
I could not believe the people that showed up the first year for the Harvester Homecoming.
It was phenomenal.
You had to wait to get in the buildings.
I mean, people all over the place and the Scouts that showed up.
The first Harvester Homecoming in August of 2019 brought out thousands of people wanting to see the hundreds of vintage International Harvester Scouts, and trucks on display.
Harvester Homecoming has become an annual festival drawing thousands of enthusiasts from all across the country.
Navistar responded by loaning its corporate collection of historic vehicles.
The festival was even able to utilize the old Scout factory grounds; the vacant engineering center was brought back to life, as former employees and their relatives walked the halls once more sharing tales of what went on at the facility.
Harvester Homecoming was a perfect name for it because it wasn't just about International Harvester in Fort Wayne.
It was about the people.
It was a family.
It is like coming home again and seeing all these people and the memories that are out there.
To me, they were the good old days.
So it's fun.
It's just wonderful to hear all the stories from the different people.
It's the people, the stories, you know, how things happened in the plants, what what was going on?
and what was your relationship with International or, or, you know, how did what job did you do?
The trucks themselves can be a source of great nostalgia, especially when there is a family connection.
All these old guys would walk up to one of the old trucks and spend 15 minutes walking around it and staring at it.
And I said, “What are you thinking” And what is, you know, is this bring back memories and the first words out of everybody's mouth after I ask that question was “my daddy”.
“My daddy drove one of these trucks”.
“My daddy used to let me ride in it.
My my daddy”, whether it was on the farm or whether it was a highway tractor, it was it.
And it's a sentimental I think that's who it is that collects these old trucks.
Is it brings back some childhood memories.
When you're doing a design, the last thing in the world you think about is that someone's still going to appreciate or have any interest in it 30 or 40 years later.
Theres not a whole bunch more things that are more important to me in my life, than preserving International truck history.
Its what I live and breathe for.
Harvester Homecoming has plans for the creation of a permanent museum to spark new connections and memories for future generations.
That is very important and I think that's going to make it live on, and I think it will.
[music] [music] For those who spent a good portion of their lives here at the Fort Wayne Works, the memories remain strong.
I liked it.
I tell you, I just love the smell.
I like the noise.
I like the people.
We work hard and sometimes we would help each other because, you know, the line kept moving.
People worked hard.
But we also had a lot of good times.
We not only worked together, we played together.
We had a close relationship.
There was just a lot of camaraderie.
Sometimes lifelong friends.
We all became very tight, close friends.
It was a family here.
I enjoyed being around them.
I forgot a lot of their names.
<Music> These folks went through something pretty serious and a lot of them, you know, they had been laid off, but they loved this company.
And that in that love of a company, you know, you just don't see that in today's environment.
You know, it was just a unique time in history, I think, in the history of the company.
It was a great company to work for.
It was a tremendous company to work for.
I was just tickled to have a job with them.
A great place to work.
It was a good place to work.
Good people to work with.
Time I started, it was like a family.
I loved working for Harvester.
I still call it International Harvester, even though it changed to Navistar.
But I'm very proud to have worked for ‘em.
I loved working here.
It was always my goal to work at Harvester.
It's just really fun.
And we just really enjoyed every day and the opportunities and the surprises.
There are always surprises.
Enjoyed all the years with Harvester.
It was hard work but the company treated us well.
It's what kept food on the table and a roof over my head.
Give me my home.
They gave me my food.
I raised three girls, put them through college.
I had four babies and a lovely wife.
And we were from good old Fort Wayne.
And I was where I wanted to be, you know?
And I'm glad I stayed there.
Certainly when I came to Fort Wayne, Indiana, which I knew very little about, to work for a truck company, I assumed I'd be here two years and go off to some wonderful place like Detroit or something.
And it just kept getting better and better.
And there was more and more reason to stay and never really seriously thought about leaving when when you come right down to it.
I can't explain how blessed we were to have the engineers we had and the understanding they had of the product in this facility, in this location.
Very central to my whole life.
I was able to spend 40 years there and enjoyed every minute of it.
I'm so blessed that I got to experience that kind of work environment with those those people.
Love them people and it's like a home away from home.
I'm just really thankful that I got the privilege of working at International Harvester, Navistar, and it gave me a good life.
Id say it was probably the the best place to work, and we were very proud of the product that we produced.
Harvester was my life.
As long as memories are passed on and passionate people continue to restore and care for the vehicles that were born here.
Fort Wayne will always remain a Truck Town.
[bittersweet music ends] [rock music] [rock music ends] [whistle blows] Truck Town: A History of International Harvester in Fort Wayne was brought to you by Hanning and Bean - a commercial real estate and property management firm invested in the development of Northeast Indiana.
Proud to support PBS Fort Wayne in preserving the legacy of International Harvester.
In 1935, Three Rivers Federal Credit Union began as a financial cooperative for the hardworking employees of International Harvester.
Committe to supporting the people, places and ideas that make our region home.
3Riversfcu.org.
O'Rourke-Schof Family Foundation.
Proud to bring the International Harvester story to the community.
Additional funding provided by Koesters Body and Frame Shop, Selking International Trucks, and the City of New Haven.
Truck Town - A History of International Harvester in Fort Wayne is a local public television program presented by PBS Fort Wayne
Hanning and Bean Enterprises Inc., 3Rivers Federal Credit Union, O’Rourke-Schof Family Foundation, Koester’s Body & Frame Shop, Selking International Trucks, and the City of New Haven, Indiana